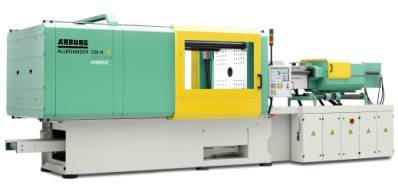
From 9 to 13 May, Arburg will present solutions for efficient injection moulding at the Brasilplast 2011 in São Paulo.As a representative of the Hidrive series, a hybrid Allrounder 720 H with a clamping force of 3,200 kN will produce flip-top caps for the packaging industry.This high-performance machine is characterised by high productivity and short cycle times.The Allrounder 320 C Golden Edition offers an especially attractive price/performance ratio.Combined with the new Integralpicker V, this economical entry-level solution demonstrates automated moulded part production using a toy car as an example.
“In Brazil, we are now one of the leading suppliers of injection moulding technology in the premium sector, and will continue to enjoy above-average growth in the future,” says Kai Wender, manager of Arburg Ltda. in São Paulo. "The Hidrive machine series has met with considerable acceptance in the local packaging market. The hybrid Allrounder machines with clamping forces from 600 to 5,000 kN are ideal for this sector, but also for all other applications that require high production capacity, coupled with precision and short cycle times."
Hybrid Allrounder 720 H: Fast, productive, accurate
The hybrid machine concept will be presented in the form of a large Allrounder 720 H with a clamping force of 3,200 kN and size 1300 injection unit. This machine from the Hidrive series combines the advantages of servo-electric and hydraulic components from the Allrounder modular component system: an energy-efficient servo-electric toggle-type clamping unit and a powerful hydraulic injection unit featuring hydraulic accumulator technology and electro-mechanical dosage. As the movement axes can be actuated independently, simultaneous movements are possible in any combination. Thanks to the generously sized injection unit in relation to the clamping force, the Allrounder 720 H boasts excellent injection performance. As overall energy consumption has been optimised, the Hidrive machines can achieve energy savings of around 40 %.
A technical application for the packaging industry will be exhibited: this injection moulding machine, equipped with a 16-cavity mould, will produce 9.5 g flip-top caps from PP in a cycle time of just 12 seconds. The material throughput is 45.6 kg/h.
Integralpicker V: No time lost during order changes
The new electric Integralpicker V will be presented on a hydraulic Allrounder 320 C Golden Edition. This low-cost robotic system, developed by Arburg, is particularly suitable for reliable sprue removal. Its servo motors also enable significant cycle time reductions. The three movement axes can be actuated simultaneously. The immersion axis, which enters the mould vertically, achieves a speed of 2 m/s at an acceleration of 20 m/s². And all this with high repeat accuracy. Since an intermediate stop, for example, and many other axis positions are programmable, the entry and removal idle times can be significantly reduced. The rotary movement for disposal of the sprue takes place within the guarding. The mould is freely accessible for conversion or service operations. The Integralpicker V is fully integrated in the Selogica machine control system. Consequently, there is just one single data record for the entire production unit. The interactive teach-in function allows fast, menu-guided set-up, with no detailed knowledge of the control system required. The robotic system is ready for operation immediately, with no need for set-up, after each order change.
Hydraulic Allrounder 320 C Golden Edition: Entry into automated moulded part production
In order to demonstrate performance using an automated entry-level machine, a hydraulic Allrounder 320 C Golden Edition with a clamping force of 500 kN and size 170 injection unit will produce a toy car at the exhibition. The wheels, chassis and roof will be produced simultaneously in a cycle time of 20 seconds. The Integralpicker V removes the individual components, which are connected to the sprue, and deposits them on a conveyor belt. Final assembly is manual.
All six sizes of the Allrounder Golden Edition, with clamping forces ranging from 400 to 3,000 kN, feature fixed clamping force/injection unit combinations. Their technically high-quality components include highly wear-resistant plasticising cylinders for a long service life, and fast-switching valve technology for high control precision and therefore high moulded part quality. Furthermore, dual-pump technology permits simultaneous machine movements and associated short cycle times. Arburg offers the Golden Edition machines with this standard equipment at an attractive price/performance ratio. They are produced exclusively at the parent factory in Lossburg – with the mark of quality “made by Arburg – made in Germany”.
As a reliable system supplier, Arburg designs and implements complete production systems all over the world. On-site project experts efficiently adapt the injection moulding machines, and all their automation and peripherals, precisely in line with specific customer requirements.
Source: Arburg.